Super Coating Solves Costly Power Plant Challenge
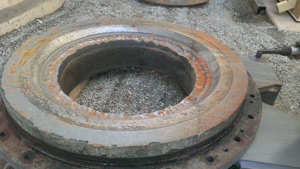
Wear plates were damaged by severe abrasion from impure water.
What’s a critical element in electricity production — one you might not immediately think of?
Water. LOTS of water.
But water used in cooling towers and elsewhere in the generation process can be highly impure if it’s from natural sources, causing severe abrasion that can lead to costly parts replacement.
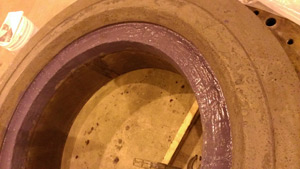
A custom coating of Belzona restored the plates to ideal condition.
One coal-fired power plant using huge volumes of river water faced a $20,000 bill every two years, just to replace two wear plates on a pump line. When they looked for a more cost-effective solution, Macomb and protective coatings partner Belzona came up with a cost- and time-saving solution.
“We have a good relationship with this power plant and they call me when they have a problem; we’re always looking for solutions for them,” says Selena Carli, General Manager of Macomb’s Carrollton Division.
That’s exactly what happened when the plant asked if Macomb could supply a coating to protect and preserve the wear plates. Selena and her team were already supplying Belzona products — two-part epoxy-based composite materials, incorporating abrasive-resistant ceramic aggregates — for other applications and customers.
“Ceramic tiles or coatings will make sure a customer gets the best lifetime out of a product without having to constantly replace it, suffer downtime and frequent maintenance,” Selena explains.
But this is not an off-the-shelf solution. The item to be protected has to be profiled for features like medium, temperature, and pressure, so the coating is perfectly fit for purpose.
Custom process
Belzona recommended a custom coating process that fit all requirements at the power plant.
“We actually put a ceramic S metal down, then filled it up with Belzona’s 1812 ceramic carbide, and then on top another coating of the S metal. That will, over time, wear off but what is underneath it, the 1812 ceramic carbide, will not,” she says.
The job cost just one-tenth of a replacement and was completed during two days of scheduled outage, though Selena says it could probably be done in 24 hours. It also avoids the hassle and order and delivery time for replacements.
Furthermore, re-coating could extend the life of the wear plates indefinitely. The Belzona material can be re-applied on-site and, with easy, step-by-step instructions, plant engineers will be able to do it themselves. Over time, the savings could be immense.
“We’re using coatings more and more in the power plant because everything’s abrasive. Their scrubber systems, limestone slurry pumps — all kinds of things wear out because they constantly have solids running through the lines and pumps,” Selena adds.
Problem solving like this, in close cooperation with our customers, builds confidence and trust. When Macomb gets to know a customer well enough to make truly helpful recommendations, it’s a true win-win.
[cta]Don’t let downtime and repeat costs hurt your business. Contact the experts at The Macomb Group by email at info@macombgroup.com or by phone at 888-756-4110.[/cta]